Korund+
Modular On-Premise computerized maintenance management system (CMMS) containing complete technical records of assets, execution of work orders covering all equipment operated by the user, monitoring and evaluation of maintenance works and management of personnel resources.
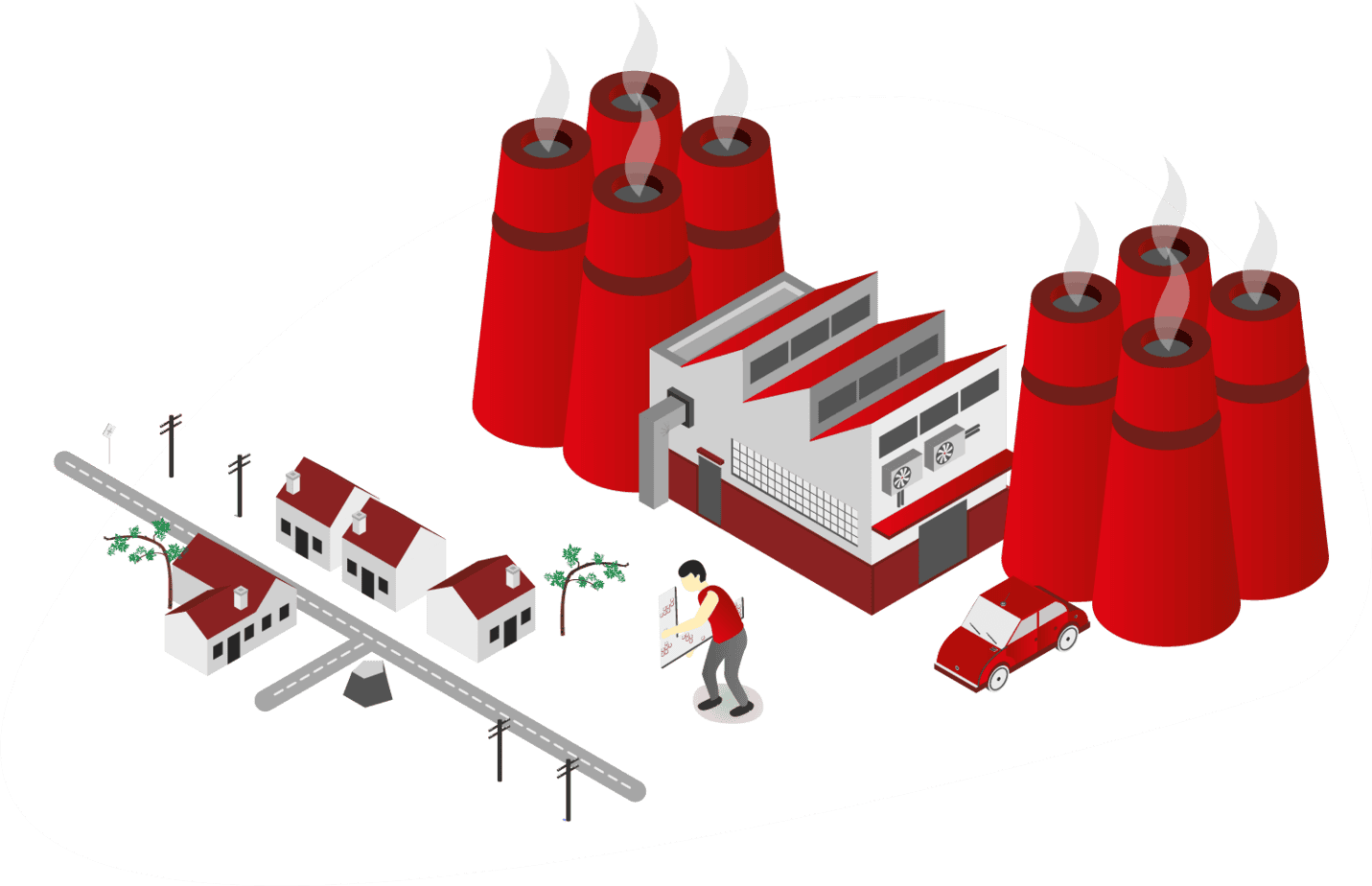
Main benefits
Korund+ software allows the operations to be as efficient as possible by applying elements of operative, preventive and predictive maintenance, by continuously monitoring and evaluating costs and the overall efficiency of the equipment.
Cost control
Monitoring and evaluation of maintenance work costs
Complexity
Comprehensive provision of all phases of maintenance works
Intertwinement with production
Methodological, technological and information intertwinement with the production process
Technical records
Complete registration and identification of maintenance objects, processes and their resources
Integration
Solution is open to be integrated with production control systems, technical diagnostics tools, data collection points, communication means, etc.
Support for maintenance life cycle
Full support for all phases of maintenance works, repairs and renovations (preparation, implementation, evaluation, optimization)
Key features
Locations
Work requests
Work orders
Preventive maintenance
Extraordinary events
Work stats
Mobile application for fast and efficient field work
It allows anyone to quickly accept a repair request and make an operative selection of the material needed to carry out the given task. It also makes it easier to compile a report on the implementation of maintenance and supplement it with the necessary photo documentation.
For more information about the mobile application, contact our sales department.
Technology
Korund+ system architecture is designed as three-layer, where the individual layers are mutually integrated into a functional unit:
Presentation layer
Multiweb
Data layer
Oracle or MS SQL Server
Application layer
MS.NET
Reference projects
Korund+
Modular On-Premise computerized maintenance management system (CMMS) containing complete technical records of assets, execution of work orders covering all equipment operated by the user, monitoring and evaluation of maintenance works and management of personnel resources.
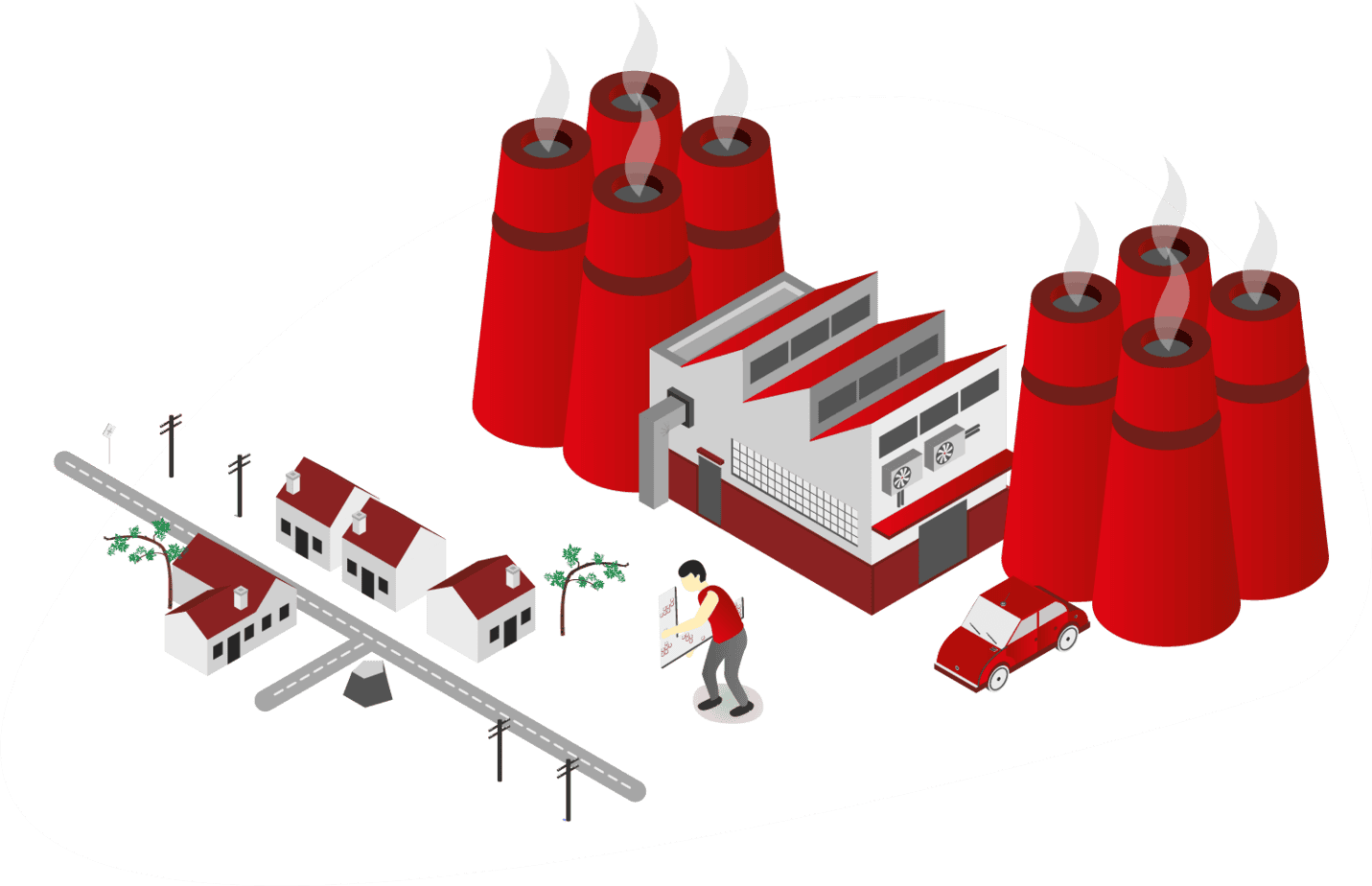
Main benefits
Korund+ software allows the operations to be as efficient as possible by applying elements of operative, preventive and predictive maintenance, by continuously monitoring and evaluating costs and the overall efficiency of the equipment.
Cost control
Monitoring and evaluation of maintenance work costs
Complexity
Comprehensive provision of all phases of maintenance works
Intertwinement with production
Methodological, technological and information intertwinement with the production process
Technical records
Complete registration and identification of maintenance objects, processes and their resources
Integration
Solution is open to be integrated with production control systems, technical diagnostics tools, data collection points, communication means, etc.
Support for maintenance life cycle
Full support for all phases of maintenance works, repairs and renovations (preparation, implementation, evaluation, optimization)
Key features
Locations
Work requests
Work orders
Preventive maintenance
Extraordinary events
Work stats
Mobile application for fast and efficient field work
It allows anyone to quickly accept a repair request and make an operative selection of the material needed to carry out the given task. It also makes it easier to compile a report on the implementation of maintenance and supplement it with the necessary photo documentation.
For more information about the mobile application, contact our sales department.
Technologie
Architektura systému Korund+ je navržena jako třívrstvá, kdy jednotlivé vrstvy jsou vzájemně integrovány do funkčního celku:
Presentation layer
Multiweb
Data layer
Oracle or MS SQL Server
Application layer
MS.NET
Reference projects
TESCO SW
QUICK CONTACT
info@tescosw.cz
tel. +420 587 333 333
tř. Kosmonautů 1288/1
779 00 Olomouc
WE CO-OPERATE
FOLLOW US
WE CO-OPERATE
FOLLOW US